ACCURL PC-2060/3000W FIBER LASER CUTTING MACHINE, TUBE CUTTING LASER
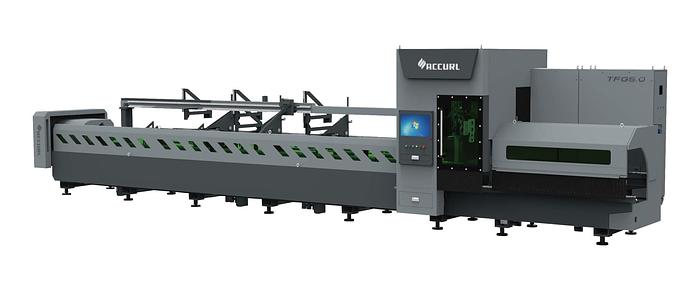
ACCURL PC-2060/3000W FIBER LASER CUTTING MACHINE, TUBE CUTTING LASER
Description
STANDARD FEATURES:
• ACCURL LASER TUBE CUTTING IS SPECIFICALLY DESIGNED FOR BUSINESSES THAT CARE ABOUT HIGH QUALITY PROFILE & TUBE CUTTING. FULL AUTOMATIC LOADING & UNLOADING REQUIRES LESS EFFORT AND TIME SAVE FOR OPERATOR.
• CAN CUT COLUMN CROSSED LINES AT THE END OF BRANCH PIPE AND MEET CENTRIFUGAL AND NON-CENTRIFUGAL VERTICAL INTERSECTION CONDITION FOR BRANCH AND MAIN PIPE AXIS.
• USER FRIENDLY GERMAN PA8000 CNC CONTROL UNIT
• IPG YLS-3000W YTTERBIUM LASER RESONATOR
• VERY EASY TO OPERATE
• QUICK AND EASY INSTALLATION
• LOW INVESTMENT AND OPERATING COSTS
• THE MOST COST EFFICIENT SOLUTION FOR EVERY REQUIREMENT
• HIGH WALL PLUG EFFICIENCY (>30%)
• ADVANCED RAYTOOLS CUTTING HEAD (WITH AIR CROSS BLAST)
• HIGH PERFORMANCE AND HIGH ACCURACY RACK AND PINION SYSTEM
• PROGRAMMABLE HIGH-PRESSURE AIR/NITROGEN GAS SELECTION 1.25 BAR
• USAGE OF HIGH-TECH BORING MACHINES FOR EXTREME PRECISION PARTS
- ACCURL CHOOSES THE BEST PRODUCTS TO GUARANTEE LONG-LASTING AND HIGH-TECH MACHINES
- ACCURL SELECTS THE BEST COMPONENTS
• BUILT IN SAFETY SYSTEMS (LIGHT GUARDS & FULL ENCLOSURE ARE OPTIONAL)
CNC CONTROL & SOFTWARE
THE PC SERIES TUBE FIBER LASER IS CONTROLLED WITH A POWERFUL GERMAN PA8000 FAMILY CNC CONTROL UNIT WHICH PROVIDES UNPRECEDENTED CONTROL OF THE CUTTING PROCESS.
CNC CONTROL UNIT
• HANDWHEEL INPUT (ONLY CN60-10K MODELS)
• EASY DATA ENTRY USING ACCURL INTERFACE, THE OPERATOR CAN EASILY AND QUICKLY IMPROVE THE CUTTING QUALITY FOR DIFFERENT TYPES OF MATERIALS
• GENERAL PURPOSE +/-10V ANALOG OUTPUT (16 BITS)
• 40 GB PROGRAM MEMORY
• ETHERNET CONNECTION
• WORLDWIDE SIEMENS SUPPORT
• 15 LCD FLAT SCREEN
• ADVANCED CORNER APPLICATIONS WITH POWER MODULATION PROVIDES PERFECT CORNERS AND SOFT CUTTING
• REMOTE DIAGNOSTIC AND SERVICE ABILITY FROM AN ACCURL LOCATION
• MACHINE QUICKLY RESTARTS FROM CUTTING INTERRUPTION POINT, AFTER POWER LOSS
RADAN 2D OFFLINE CAD/CAM SOFTWARE
THE PROGRAM CAN BE COMPLETELY CREATED OFF-LINE, USING CAD/CAM SYSTEM METALIX OR LANTEK.
• THE GEOMETRY OF THE PIECE TO BE CUT BE DIRECTLY DRAWN OR IMPORTED FROM OTHER CAD SYSTEMS (IN DXF OR IGES ETC.)
• A DATA BASE MAKESTHE MANAGEMENT OF THE TECHNOLOGY TABLE EXTREMELY EASY, (OFFLINE SOFTWARE CLASSIFIES PARTS SIZES)
• AUTO-NESTING ALLOWS THE OPTIMIZATION OF THE MATERIAL, BY AUTOMATICALLY DEFINING THE LAY-OUT OF THE FIGURES TO BE CUT WHICH EXPLOITS THE SHEET METAL TO THE MAXIMUM
• FULL-AUTOMATIC CUTTING. (ANY CAD DRAWINGS CAN BE IMPORTED TO CREATE NC CODES WHICH ARE LOADED TO THE CONTROLLER VIA NETWORK OR MEMORY STICK). INITIATION OF THE PROGRAM BY PUSHING START BUTTON ONLY.
• COMMON CUT-COMMON BORDER OF PARTS REDUCES CYCLE TIMES AND MATERIAL DEPOSITS BY CUTTING ONCE
• FAST HEAD PATH COLLISION PROTECTION
• REAL FONT STYLES ARE SUPPORTED TO CUT OR MARK
• PRE-PIERCING FINISHES ALL PIERCINGS PRIOR TO CONTOURS
• SPRINT CUT CHOOSES THE SHORTEST PATH OF HEAD FROM ONE TO ANOTHER CONTOUR
CENTERING CHUCK
TO GET CUTTING PRECISION, CENTERS THE PROFILE AS CLOSE AS POSSIBLE TO THE CUTTING HEAD. DRIVER TURN SYNCRONIZED WITH CHUCK. 4 INDEPENDENT CLAMPS COMES TO POSITION AUTOMATICALLY BEFORE PROFILE CONTINUES.
TUBE CENTERING MECHANISM
TUBES CENTERING MECHANISM, WHICH IS ON THE FIRST SUPPORT TAKES TUBES TO THE CHUCK AXIS.
HYDRAULIC PROFILE HOLDER
IT CAN HOLD A VARIETY OF PROFILES BY 4 CLAMPS WORKING INDEPENDENTLY AS 2+2. ADJUST HYDRAULIC PRESSURE AUTOMATICALLY ACCORDING TO THE PROFILE MATERIAL THICKNESS.
CUTTING HEAD WITH Z AXIS
THE Z AXIS ALLOWS FASTER CUTTING PROCESS WITH ITS HIGH DYNAMIC PERFORMANCE. LASER HEAD WITH AUTOMATIC FOCUSING ELIMINATES TIME LOSS IN THE PREPARATION PHASE BEFORE CUTTING.
RACK AND PINION MOTION SYSTEM
THE HIGH PRECISION TWO-DAY, HARDENED HELICAL RACKS WITH LOW CLEARANCE MAKE IT POSSIBLE TO ACHIEVE VERY HIGH ACCELERATION (10M/S2), SPEED (100 M/MIN) AND ACCURACY (0.05MM) VALUES.
TECHNICAL SPECIFICATIONS:
• DIMENSIONS (L x W x H) 14500 x 5250 2250 MM
• CUTTING DIAMETER 20-210 MM
• TUBE LENGTH 6500 MM
• LASER SOURCE WAVELENGTH 1070-1080 NM
• LASER POWER OUTPUT RANGE 0.2-3KW
• LASER POLARIZATION RANDOM
• LASER MAX. PULSE FREQUENCY 5 KHz
• MAX. PIPE DIAMETER 350 MM
• MAX. SQUARE PROFILE DIMENSION 300 x 300 MM
• MAX. RECTANGULAR PROFILE DIMENSION 280 x 210 MM
• MIN. PIPE-PROFILER DIAMETER 25 MM
• MAX. PROFILE LENGTH 6000 MM
• MAX. PROFILE WEIGHT 38 KG/M
• MAX. TOTAL WORKPIECE WEIGHT 310 KGS
• MAX. BUNDLE WEIGHT 4000 KGS
• MAX. MATERIAL THICKNESS 8 MM
• MIN. MATERIAL THICKNESS 0.6 MM
• AMOUNT OF CHUCK 1
• CENTERING CHUCK YES
• LAST CUT PROFILE LEFT LENGTH 40
• DRIVER MIRROR LINEAR VELOCITY 120 M/MIN
• DRIVER MIRROR LINEAR ACCELERATION 10 M/S2
• POSITIONING ACCURACY +/-0.2 MM
• REPEATABILITY +/-0.05 MM
• PROFILES CAN BE CUT ROUND, SQUARE,
RECTANGULAR, ELIPTIC H,
C,U L, I
OPTIONAL ACCESSORIES:
• AUTOMATIC LOADING AND UNLOADING SYSTEM
• CARTRIDGE DUST COLLECTOR FOR FILTER WLC-6YT
• ACCURL COMPACT LOADING SYSTEM
• SCREW AIR COMPRESSION ZLS15A
AUTO LOADING SYSTEM
THE PROFILES TAKEN FROM BUNDLE ONE BY ONE TO THE CHAIN, SYSTEM MOVES THE PROFILES UP AND GRIPPERS CLAMP THE PROFILE AND MOVE IT TO THE CHUCK AXIS AND THE CHUCK HOLDS THE PROFILE.
LOADING ARM
• PROFILE LOADING IS MADE BY LOADING ARMS OUTSIDE THE COVER
• PROFILE THAT PLACED TO LOADING ARM AUTOMATICALLY MOVE TO THE CUTTING AREA AND IS CENTERED
• DURING CUTTING THE NEXT PROFILE IS PLACED IN THE LOADING ARM TO SAVE TIME
• DURING LOADING COVERS OPEN AND AFTER LOADING ARE CLOSED FOR PROTECTION FROM THE LASER BEAM
• LIGHT BARRIER FOR THE LOADING ARM DOES NOT STOP THE MACHINE, ONLY STOPS THE LOADING ARM
CENTERING MIRROR
• TO GET CUTTING POSITION, CENTERS THE PROFILE AS CLOSE AS POSSIBLE TO THE CUTTING HEAD
• DRIVER TURN SYNCRONIZED WITH MIRROR
• 4 INDEPENDENT CLAMPS COME TO POSITION AUTOMATICALLY BEFORE PROFILE COMES
• CENTERING MIRROR MOVES FORWARD AND BACKWARD ON RACK AND PINION. BECAUSE OF THE FORWARD MOVE THE LASER HEAD GOES BEHIND THE MIRROR AND MIN.
• LEFT MATERIAL ACHIEVED ON THE LAST PROFILE CUT. BECAUSE OF THE BACKWARD MOVE WITH SENSOR AT MIRROR, LOADED PROFILE ZERO POINT MEASURED AND SENT TO THE SYSTEM.
HYDRAULIC PROFILE HOLDER
• IT CAN HOLD A VARIETY OF PROFILES BY 4 CLAMPS WORKING INDEPENDENTLY AS 2+2.
• ADJUST HYDRAULIC PRESSURE AUTOMATICALLY ACCORDING TO THE PROFILE MATERIAL THICKNESS.
• WITH LASER SENSOR ON IT MEASURES PROFILE LENGTH AND SENDS THE DATA TO THE SYSTEM
UNLOADING UNIT
• UNLOADING UNIT SUPPORT MECHANISM HEIGHT IS CONTROLLED BY THE SERVO MOTOR AND KEEP SUPPORT PROFILE DURING CUTTING
• BECAUSE OF UNLOADING TABLE THAT MOVES FORWARD AND BACKWARD THROUGH PROFILE, CUT PROFILE PARTS CAN BE RELEASED TO DIFFERENT TABLES ACCORDING TO THEIR LENGTHS.
Specifications
Condition | New |